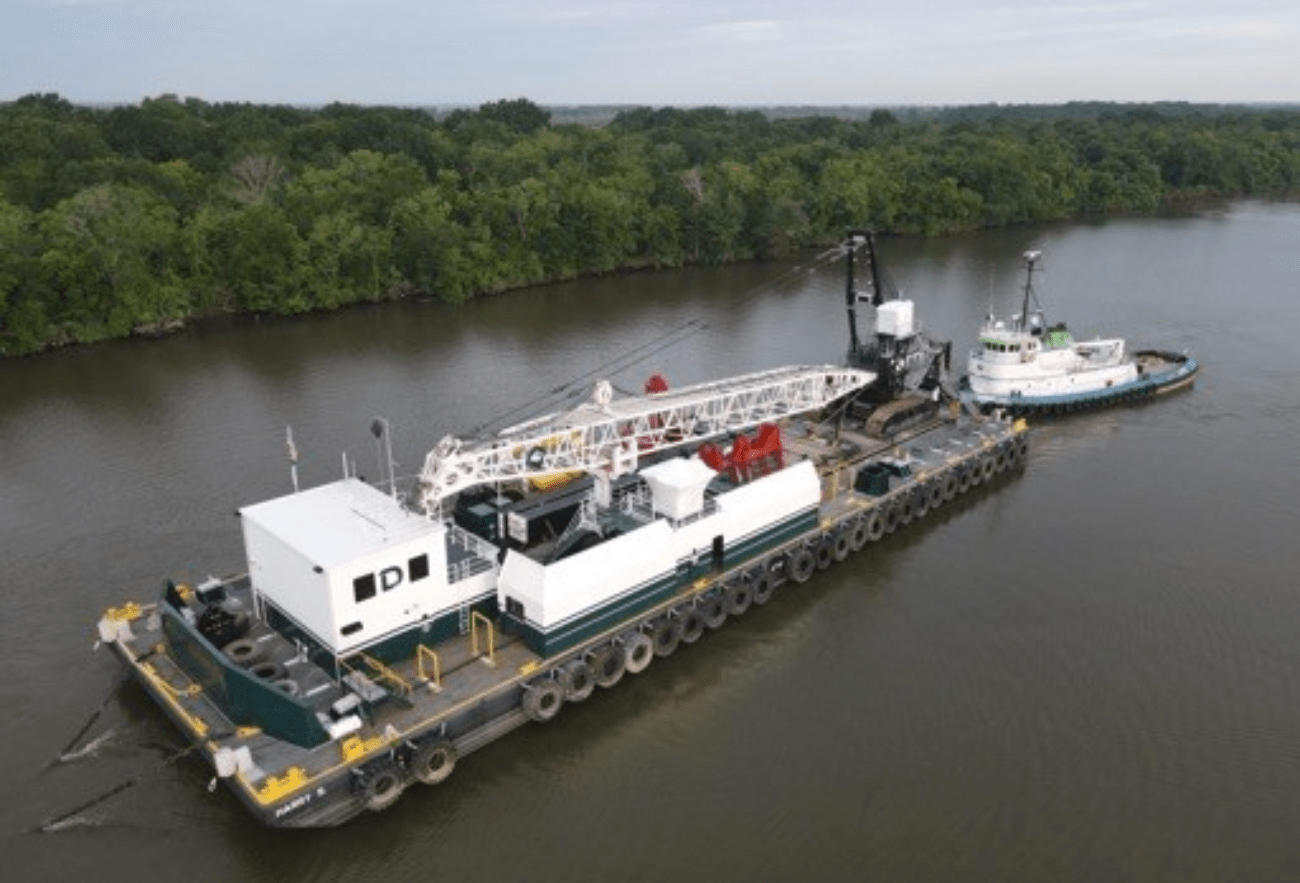
Harry S: The Dutra Group’s Innovative and New Crane Barge
The road to building the new Harry S crane barge—named after the company’s longtime COO (and recently appointed CEO) Harry Stewart—began with an intensive three months of design and engineering planning involving CEO Bill Dutra, COO Harry Stewart, VP of Equipment Steven Lee and Fleet Manager Dennis Ferguson in early 2021. The foursome set out to model the new crane barge after its highly functioning predecessor, the Paula Lee, but with several key changes.
Building a crane barge, not to mention the largest one in the fleet, is no easy task in ordinary times; however, the last few years have been anything but ordinary. The entire buildout process of the Harry S was intensified by an undercurrent of complexities, both expected and unexpected, involving supply chain issues, illnesses, forces of nature and other challenges.
The Harry S design team wanted the barge to fit Austrian manufacturer Liebherr’s largest duty-cycle 300-ton crane, the HS 8300 HD. “However, the crane was lighter than what we wanted,” said Lee, “so we collaborated with Liebherr’s engineering team to increase the HS 8300 HD’s capacity to meet our specific needs, including addressing its counter-weight size, pedestal height and track width, plus making a few other adjustments. It added 50 more tons to the finished product.”
Once the crane build-out was decided upon, the team conducted a stability analysis to determine the barge size and how the entire vessel would operate not only in today’s climate, but also for many years to come. The strategy was centered on building a barge that could accommodate a larger crane in the future, after the modified HS 8300 HD crane reached its useful life anywhere from 7 to 10 years in the future.
We collaborated with Liebherr’s engineering team to increase the HS 8300 HD’s capacity to meet our specific needs, including addressing its counterweight size, pedestal height and track width plus making a few other adjustments. It added 50 more tons to the finished product.”
The Dutra team also added the latest tier-compliant engine available, including a pactronic accumulator system to bolster a 1,000 horsepower engine to provide the equivalent of 1,600 horsepower worth of working energy. Additions of electronic and navigational aids were made to the cab to give operators a more accurate view of the underwater bucket location.
Although smaller in size than the Paula Lee, the Harry S has 10 percent more capacity in terms of greater cycle rates and production rates than the Paula Lee, uses approximately half the fuel load, and is the largest crane barge in the company’s extensive fleet.
The Harry S was also outfitted with the latest technology to enhance safety protocols and to ensure the crane is 100% wirelessly connected to the barge via bluetooth and wifi at all times.
The barge build-out utilized all the latest in design tools and manufacturing methods, including AutoCAD design software, use of CNC machines for steel cutting, modularization for accuracy in the building process and NDT (non destructive testing) to check weld porosity and to evaluate properties of the materials.
Once the crane was finished, it was shipped from Austria to the Port of Galveston in Texas, and then transported by truck to Amelia, Louisiana. A team of two dozen workers set about to assemble it for the already completed barge—a move that enabled the crew to better familiarize themselves with the vessel and to have a level of participation and ownership. The newly completed vessel met all SOLAS (Safety of Life at Sea) regulations as stipulated by both the US Coast Guard and the American Bureau of Shipping.
Completed both on-budget and on-schedule in just under a year, the Harry S was commissioned into service in June 2022. Although smaller in size than the Paula Lee, the Harry S has 10 percent more capacity in terms of greater cycle rates and production rates than the Paula Lee, uses approximately half the fuel load, and is the largest crane barge in the company’s extensive fleet.
Facing The Challenges Imposed By A Global Pandemic
Anyone involved in manufacturing has experienced the supply chain woes of the past two and half years. For Dutra, building a 1110-ton barge came with its own share of challenges, starting with delays and shutdowns of raw material exportations to manufacturing-centric countries, along with factory closures around the world, all of which created a highly fractured and broken manufacturing chain. “For our project, it became a constant juggling act to procure and expedite the materials in the order they needed to be in,” said Lee. Steel prices were also constantly rising, but the team had the foresight to lock in steel prices under contract to avoid escalations.
The challenges persisted on the homefront too, with Covid-related illness impacting team members and creating additional difficulties. The team grappled with extreme heat—up to 110 degrees some days— in Southeast Louisiana, where the crane was assembled. Adding insult to injury, Hurricane Ida reached Louisiana in late August 2021, causing widespread damage and power outages throughout the area.
Keeping it “In The Family”
The Dutra Group’s family values include the long-held tradition of naming fleet vessels after company employees. The Stewart family name is integrated throughout the fleet; before the Harry S there were three existing dump scows named after Harry’s daughters: KS-10 for Kaitlyn, ES-15 for Ellyn and MS-16 for Maddy. In 2023, a tugboat will be named the Kimberly S after Harry’s wife.
“The Harry S was designed and built with the future of The Dutra Group in mind,” said Lee. “We had the foresight to assemble a barge with the size and stability we will need to withstand the next generation of crane once it becomes available.”