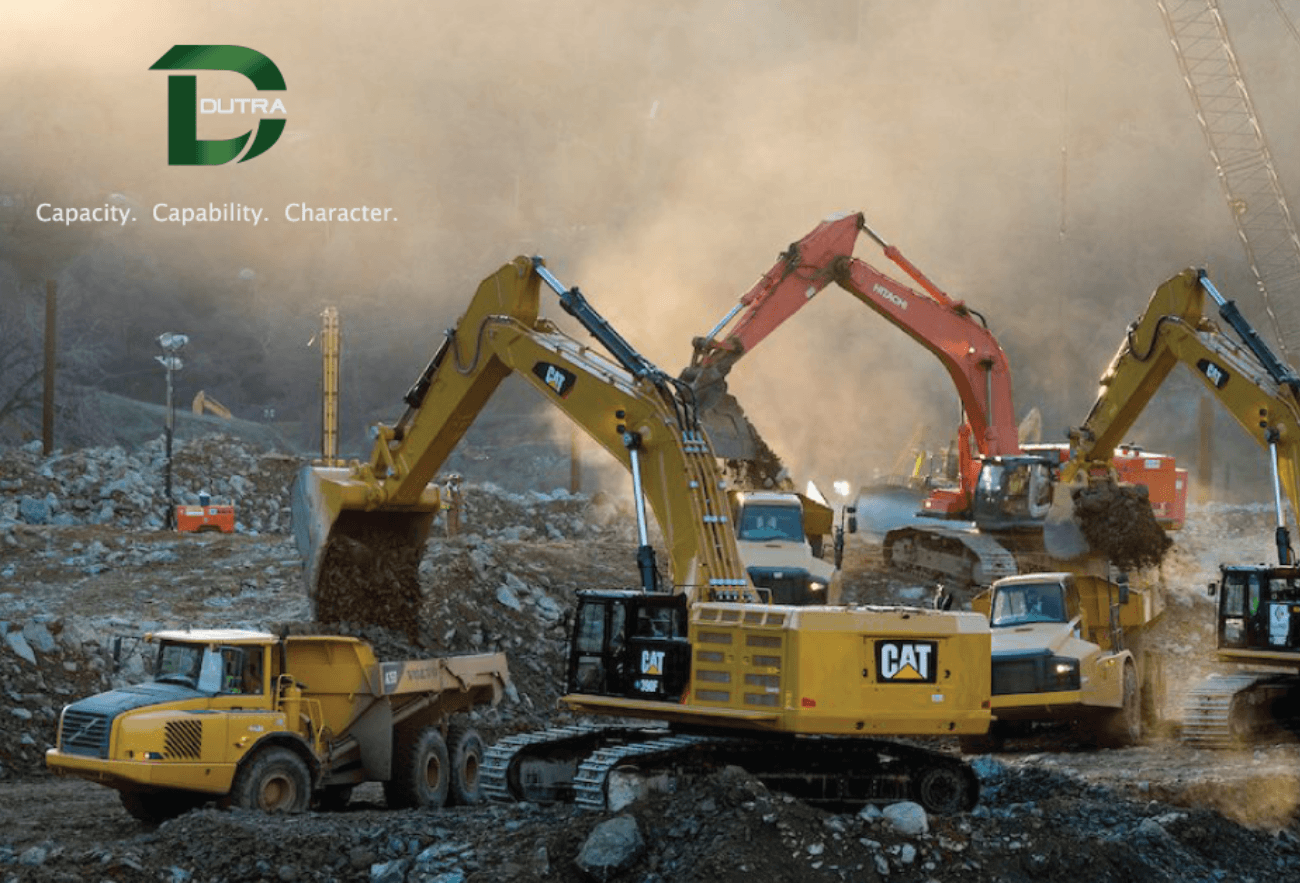
Navigating Challenges: A Year of Collaborative Success
2022 has been a year where collaboration and cooperation with corporate, vice presidents, managers and field personnel were keystones and allowed us to block and tackle through the year’s challenges successfully. It is a testament to the leadership of The Dutra Group to huddle up to overcome those challenges whether they be economic, scheduling, inclement weather, supply chain issues or a third year of COVID.
When we think of supply chain issues, we tend to think of container ships stacked up at ports and shortages of household goods. Aside from those visions, the challenges they pose to manufacturing and repairing of equipment can be broken down into a few examples.
During the past three years, much of the world was either working remotely or factories were shut down completely due to Covid lockdowns. The global manufacturing segment was drastically affected by these worldwide closures. Many manufacturers stated that erratic demand patterns led to inadequate control over internal operations and created imbalances in supply and demand, making things complex and disruptive. Delays in raw material exports to equipment and machinery manufacturers, along with lockdowns at factories in China, South Korea, Taiwan, Vietnam and Europe, stressed already-lean inventories of myriad required items, many of which needed to be pre-ordered far ahead of needs.
A second example is OEMs (original equipment manufacturers) taking over the outsourcing of components in order to stop flying blind on arrival dates of materials and machinery needed for their own manufacturing processes. For instance, our new Liebherr 8300.2 crane, which was built by Liebherr in Nenzing, Austria, is made of outsourced winches, hydraulic components, and dozens of other vendor contributed materials. The paint used on several of our dry-docks this year was impacted by shortages of mineral and material exports to paint manufacturers here in the US. The paint used on vessel hulls is made of more than 27 chemicals; manufacturer shortages of even one of those chemicals lowered inventory levels and caused the U.S. Navy to lock down US manufacturers’ distribution to the industry, which in turn limited commercial availability. In addition, the price of steel during that same period more than doubled (thankfully we are now seeing a rebound in pricing and availability). But when steel mills were either shut down or had minimized their production, many mills refocused efforts on manufacturing higher margin products such as automotive gauge steel products and other goods that fell outside our industry’s needs.
The above summary of parts/materials/labor supply chain disruptions illustrates the many challenges we needed to overcome at several drydocks this year on dredge Stuyvesant, scow WF9, scow KS10, tugboat Sarah Reed, crew boat Gracie Jean, workboats Linda T and Phyllis T—plus other projects within our company. We encountered additional challenges with supply and labor force availability during our new builds of scow MS16 and crane barge Harry S; still, both builds were successfully completed on schedule and are currently on projects. Our new workboat Kimberly S is on track to be delivered in February 2023.
Many thanks to the corporate, legal, VPs, safety, purchasing, finance and accounting, estimating and operations teams for their “whole village” effort this year.